A recent project saw us revisit an old drilling site to carry out some improvement works on a third party system that had been installed after our works were complete.
Back in 2009 we were commissioned by a large factory site to drill two large abstraction boreholes at 12” diameter to 110m deep each. Once installed the boreholes provided a large flow of water i.e. in excess of 80m3/hr each. The use of the water was for an industrial process and it resulted in significant cost savings when compared against the cost of mains water supply.
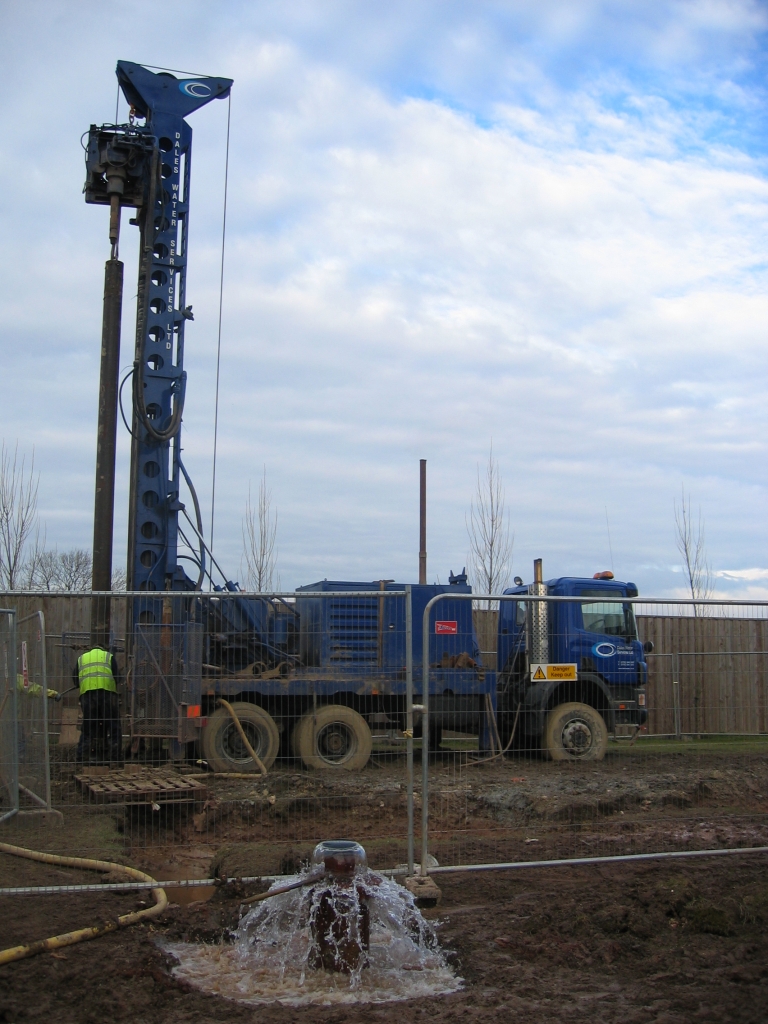
Boreholes being constructed in 2009
At the time we were only commissioned by the factory site to construct the boreholes. Another firm was brought in at a later date to design and install the pumping solution for the boreholes and pipework infrastructure.
Fast forward to 2015 and we were contacted by the site asking if we could assist them with the pumping installation which had never properly worked and was now in a very poor condition.
The existing system installed by the third party comprised of two large variable speed suction pumps on a duty standby basis with a third smaller variable speed pump to accommodate the low flow requirements. The system operated by transfer from the low flow pump on to which ever high flow pump was in service at the time as demand for water increased in the factory.
Suction pumps do have their uses but when compared to a submersible pump specifically designed for a borehole situation they have the following drawbacks:
- Water is being pulled rather than pushed which is a less efficient and can’t be delivered at a constant rate.
- Should the water level in the borehole decrease there becomes a point at which sucking or pulling water can’t occur any more as gravity beats the ability to do this. In context of a borehole this means that as the water level is depressed through pumping the suction pumps will eventually not be able to ‘suck’ anymore and pull in air.
- Pumping from depth will assist in developing the boreholes from depth.
- Suction pumps use more electricity, they’re much noisier and wear out quicker.
- Less flexibility or scope for ever changing requirements or expansion.
Because suction pumps significantly decrease the pressure in the water being pumped, this creates what’s known as “cavitation” where the liquid turns into a vapor. The effects of the above and cavitation had almost destroyed the suction pumps and a new solution was required. Furthermore, the pipework which had been installed was galvanised steel and had rotted away.
Our Solution
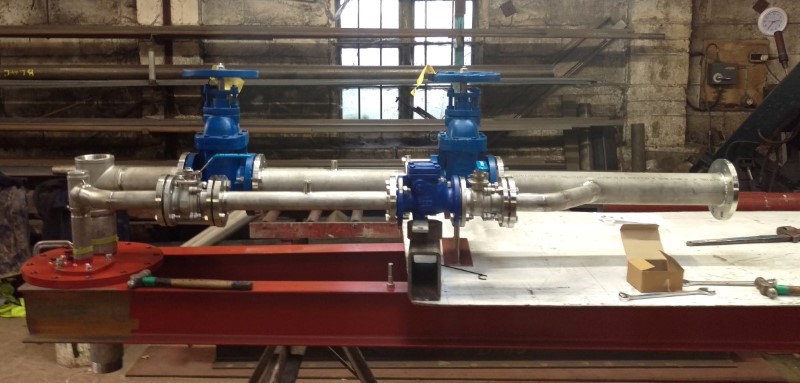
In the workshop
After discussion and working with the client it was concluded that a superior borehole submersible pumping installation would be installed utilising a small submersible pump combined with a larger submersible pump in each borehole.
Each borehole would be on duty standby, transferring on a weekly basis to share the demand evenly. The small pumps would seamlessly transfer the low demand on variable speed to the larger pump when demand for water increased in factory. The design was set and it was also concluded to renew all the rotten above ground pipework with new stainless steel pipework.
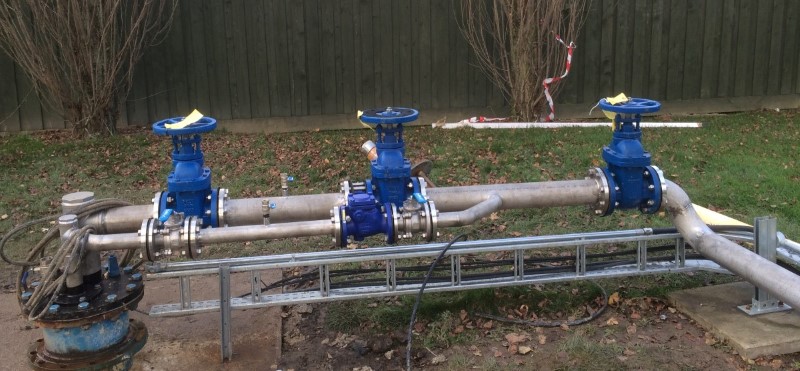
Part Way Through Installation
The installation took place when the factory was shut down meaning no downtime and the system commissioned. An added benefit has also seen the reduction in the size of the submersible pump motors compared to the old suction pumps. The factory now has a great pumping solution to maximise their borehole water usage, the capital costs quickly being recouped compared to mains water costs and reduced electricity bills compared to the suction pumps.
Works Complete
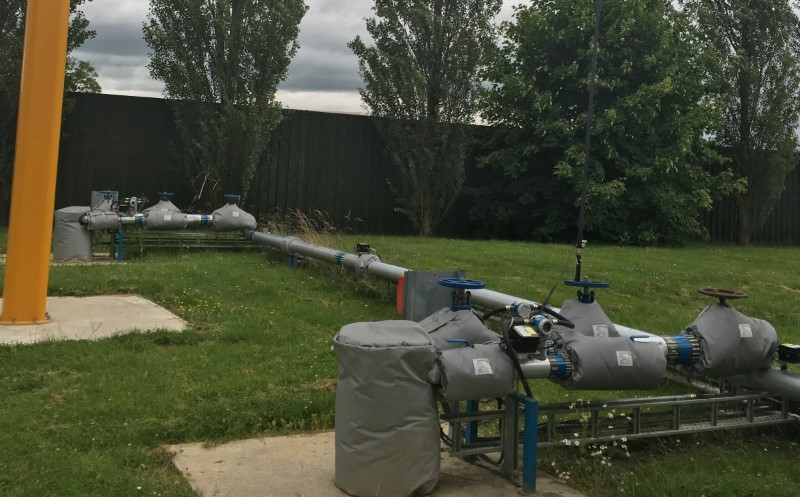
The Finished Article
- Boreholes constructed that deliver a large volume of water
- New pumping installation designed and installed
- Working with clients to meet their needs and add our expertise
- Identifying problems and finding solutions
- Installing the best technology to maximise returns
- New pumps installed
- Minimised electricity bills
- No more pump cavitation
- New stainless steel pipework
- Full meetings to coordinate works before, during and post installation
- A happy client!
An all-round a successful project. If you require assistance with your borehole or pumping installation project feel free to contact us with any questions you may have.